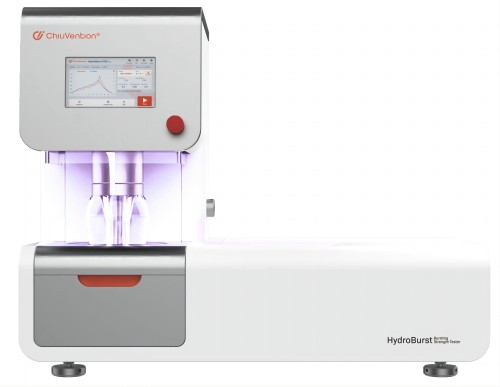
Introduction
When it comes to evaluating the strength and durability of fabrics, burst testing is one of the most critical quality control procedures. The bursting test of fabric measures a material’s resistance to pressure and its ability to withstand force before rupturing. This test is particularly important for textiles used in high-stress applications, such as industrial fabrics, medical textiles, protective clothing, and upholstery.
Understanding different burst testing methods helps manufacturers ensure product reliability, compliance with industry standards, and customer satisfaction. This article explores the significance of burst testing, common testing techniques, industry standards, and factors affecting test results.
Why is Burst Testing Important?
The bursting test of fabric provides valuable insights into a material’s structural integrity. Unlike tensile testing, which measures strength in a linear direction, burst testing evaluates multidirectional stress resistance, mimicking real-world conditions where fabrics experience pressure from multiple angles.
Key applications of burst testing include:
Apparel & Sportswear – Ensures fabrics can withstand stretching and pressure during use.
Medical Textiles – Verifies the durability of surgical gowns, compression garments, and bandages.
Industrial Fabrics – Assesses materials used in geotextiles, filtration, and protective gear.
Upholstery & Automotive Textiles – Determines resistance to wear and tear in seating and interiors.
By conducting burst testing methods, manufacturers can prevent product failures, reduce returns, and maintain compliance with international safety standards.
Common Burst Testing Methods
Several standardized techniques are used to perform the bursting test of fabric, each with specific advantages depending on the material and application. The most widely used methods include:
1. Hydraulic Bursting Strength Test (ASTM D3786 / ISO 13938-1)
This method applies hydraulic pressure to a fabric sample until it bursts. A rubber diaphragm expands using liquid pressure, exerting force evenly across the material.
Procedure:
A circular fabric sample is clamped between two plates.
Hydraulic pressure increases gradually until the fabric ruptures.
The burst strength is recorded in kilopascals (kPa) or pounds per square inch (psi).
Advantages:
Suitable for heavy fabrics like denim, canvas, and industrial textiles.
Provides consistent and repeatable results.
2. Pneumatic Bursting Strength Test (ISO 13938-2)
Similar to hydraulic testing, this method uses air pressure instead of liquid to expand a diaphragm and apply force to the fabric.
Procedure:
The fabric is secured in a clamping device.
Compressed air inflates the diaphragm until the sample bursts.
The maximum pressure is recorded.
Advantages:
Faster than hydraulic testing.
Ideal for lightweight and stretchable fabrics like knits and spandex.
3. Ball Burst Test (ASTM D6797)
This method uses a steel ball to puncture the fabric, measuring its resistance to penetration. It is commonly used for upholstery, automotive textiles, and protective clothing.
Procedure:
The fabric is clamped over a circular opening.
A 25mm or 38mm steel ball is pressed into the fabric at a constant speed.
The force required to burst the fabric is recorded in Newtons (N).
Advantages:
Simulates real-world puncture scenarios (e.g., sharp objects, high-pressure contact).
Useful for coated and laminated fabrics.
4. Diaphragm Bursting Test (BS EN ISO 13938-1)
This variation of hydraulic testing uses a flexible diaphragm to apply pressure uniformly. It is widely used in European standards.
Procedure:
The fabric is clamped, and hydraulic pressure expands the diaphragm.
The burst strength is measured when the material fails.
Advantages:
Highly accurate for woven and nonwoven fabrics.
Compatible with multiple international standards.
Industry Standards for Burst Testing
To ensure consistency and reliability, various organizations have established standards for burst testing methods:
ASTM D3786 – Standard test method for hydraulic bursting strength of textiles.
ISO 13938-1 & 13938-2 – International standards for hydraulic and pneumatic burst testing.
BS EN ISO 13938-1 – British/European standard for diaphragm burst testing.
ASTM D6797 – Standard test method for burst strength of nonwoven fabrics using a ball burst apparatus.
Compliance with these standards ensures that test results are comparable across different laboratories and industries.
Factors Affecting Burst Test Results
Several variables can influence the outcome of a bursting test of fabric, including.
Fabric Composition – Natural fibers (cotton, wool) behave differently than synthetics (polyester, nylon).
Weave or Knit Structure – Tight weaves generally have higher burst strength than loose knits.
Fabric Thickness – Thicker materials typically withstand higher pressures.
Moisture Content – Wet fabrics may show different burst resistance compared to dry ones.
Testing Speed & Pressure Rate – Faster pressure application can lead to lower burst strength readings.
Manufacturers must control these factors to obtain accurate and repeatable results.
Conclusion
The bursting test of fabric is a vital quality assessment tool that ensures textiles meet performance and safety requirements. By employing different burst testing methods—such as hydraulic, pneumatic, ball burst, and diaphragm tests—manufacturers can evaluate fabric durability under various conditions.
Adhering to international standards (ASTM, ISO, BS EN) guarantees consistency, while understanding influencing factors helps optimize fabric development. Whether for apparel, medical textiles, or industrial applications, burst testing remains a cornerstone of textile quality control.
Investing in precise burst testing methods not only enhances product reliability but also builds consumer trust in the longevity and safety of textile products.
For more information on textile testing methods/standards
or textile testing machines, contact us:
What’s App: +86 180 2511 4082
Tel: +86 769 2329 4842
Fax: +86 769 2329 4860
Email: sales@tes.hk